Contractor Stories
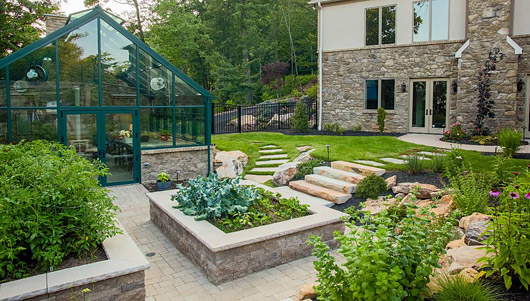
Years consumed on 1 project
Failures by a past contractor lead to trial projects then to 2+ years of non-stop work creating an award winner.
By Tom HatlenThis story starts 4 years before Tim Langletz first set foot on the property that would become his largest project to date. The house was under construction and the homeowner had gotten 2 prices on landscaping, one from a well-known, respected contractor and one that was $80,000 cheaper.
Profile
2013 HNA Project Award Winner
Harrisburg, PAConstruction & Design Company
PA Landscape Group, Inc.New Cumberland, PA
Project Manager
Tim Langletz, President / Brendan Hoover, COO
Designer
Tim Langletz, President / John Otterson, Landscape Architect
Property size
4 acresLandscaped area
1-1/2 acresProject value
$495,000 – Price includes all grading, pavers, walls, steps, outdoor kitchen, outdoor living room, water features, bridges, planting, irrigation, sodding, lighting, swale construction, boulder and drainage work.Work done by others
Natural gas installationGreenhouse construction
Drainage canal excavation
Fencing
Parts of the fireplace
Year completed
2013 (Additional work is ongoing.)And, guess what happened.
It started with a pond-less waterfall that didn’t work. The basin wasn’t near large enough to hold anything but a tiny pump and a fraction of the water the water feature required. “Plus it was all clogged up and looked artificial,” reflects Tim.
Elsewhere, there were cracking travertine pavers that were laid incorrectly with no base material. “They were moving all over the place. It was cracking because travertine is so porous that it holds water and doesn’t hold up with the freeze/thaw cycles that we have here.”
And, the gas grill never worked because the gas lines weren’t installed right. “We had to redo a gas line all the way around the house.
“There were water pipes missing. We had to change all sorts of grades, and rip everything out. It was a nightmare.”
But, the biggest problem was the retaining wall that crashed. The wall was 6’ tall built with small blocks, improper backfill stone, no geogrid and a drainage canal just 4’ behind it.
The wall was still standing that day Tim first visited the property. “When I saw it, the first words out of my mouth were, ‘That wall's going to fail.’ And I told him why. I could see the ends just stopped instead of wrapping around and going back into the bank. I could tell by the profile how it was built.”
Within months, heavy rains came crashing down the canal from the mountain above the property, and the wall was toast.
“Test” projects build client confidence
But Tim’s 1st project for the client was to rebuild that waterfall. It was 1 of several smaller jobs Tim viewed as test projects for the client to become comfortable with his work.After the water feature, PA Landscaping rebuilt the outdoor kitchen island, and added the pergola and the trellises in the pool area. Then the wall failed, and they began reworking that area.
Trust had grown to the point where the client actually asked PA Landscape to develop the plan for the placement of a huge new garage/gym addition, “And how that would work best with the property. But he wasn't going to do anything more with the backyard yet. Then his stepdaughter wanted to get married at the house. That's when he pulled the trigger on the whole project.”
2+ years consumed by 1 project
The whole project was initially planned be done piecemeal over a 4-year timeframe. But, working on it full-time with the help of 2 mild winters, they finished it in 2-1/2 years with 5,300 man-hours logged in. Two 3-man crews worked different sections of the hardscape part of the project at the same time. An additional landscaping crew worked on other areas.Tim says, “This job stretched us to the max. We had to buy 2 new pieces of machinery. We bought a mini excavator and another skid steer because we needed them on that job every day.
“It got to a point where I'd be over there every Saturday eating breakfast with them and going over the project. As soon as we did one piece of the job, he'd say, ‘Can we also do this too?’ Then we’d have to figure out how to make it work with the rest of it. The project kept growing and growing and growing.”
Because the job was always changing, Tim steered the client to time-and-materials pricing. “I said, ‘I can price out a bid for you, but this is such a complex job, I’ll need to bid it for all the hidden costs.’ I said, ‘I think I can be fairer to you if we give you some budgetary figures as we go along, and we charge time and materials for just what we do.’”
This was the last big project where Tim served as the project manager. Chief Operating Officer Brendan Hoover now handles those duties. Tim says building the infrastructure for the job was the hard part.
“Getting the grades set and getting all the piping in and everything that's underground right so it will all come together in the end … That's where all the time and thought goes. Laying pavers is simple.”
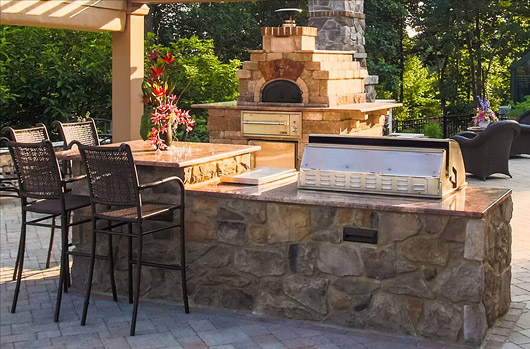
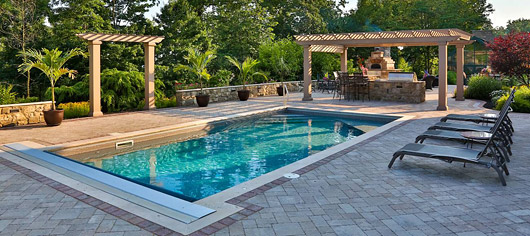
The pool was one of the few things salvaged from the previous landscape. The outdoor living room and fireplace is just behind the kitchen area. The greenhouse is beyond that.
![]() | ![]() |
A natural stone staircase delivers visitors from the breezeway and drive above down to the outdoor living room and fireplace below. The outdoor kitchen and pool are to the left of the fireplace. The greenhouse is to the right. The steps are staggered right and left to provide character. The stone is Western Mountain Stone cut and faced near Scranton, PA.
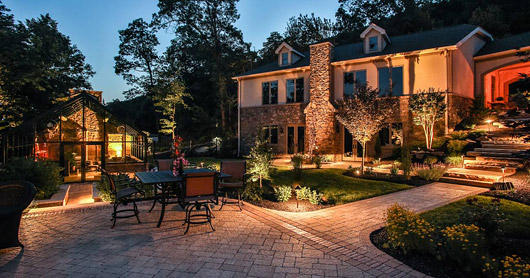
Upwards of 200 low voltage LED lights illuminate the project. Tim says, the greenhouse interior was so decorative, “I wanted to light it from the inside – not from the outside – so that you could see the inside of the greenhouse. We wanted the greenhouse back wall to look like an existing old wall that we attached the greenhouse to. The wall serves as a backdrop. We didn't want to see through to the neighbor's yard.”
The large structure in the upper right is not the house. It’s the new garage/gym addition. The breezeway to the far right provides access to the backyard and connects to the house.
The large structure in the upper right is not the house. It’s the new garage/gym addition. The breezeway to the far right provides access to the backyard and connects to the house.
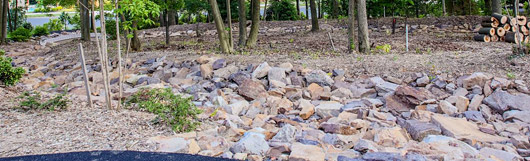
PA Landscaping built stone swales the length of the property to take runoff down to the street drains. Tim says the swales are 12’ wide in some places. “We designed it so all the upper driveway water and downspouts dump into the swales, eliminating the washouts that plagued the site.
“We've done 5 houses on this mountainside, and we knew we were going to have water issues up there. We ran into a lot of springs. We had to find the source and pipe them into the swales. Without the swales, water would run all the way down and wash out everything onto the sidewalk and street.”
“We've done 5 houses on this mountainside, and we knew we were going to have water issues up there. We ran into a lot of springs. We had to find the source and pipe them into the swales. Without the swales, water would run all the way down and wash out everything onto the sidewalk and street.”
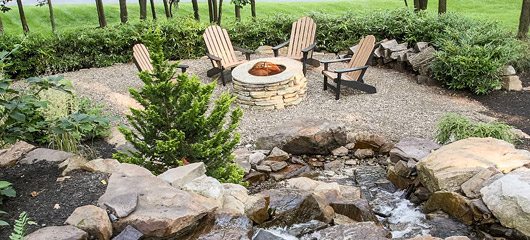
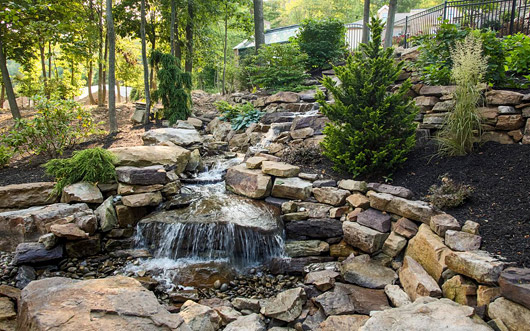
This waterfall is located down below the outdoor kitchen/pool area. It was PA Landscaping’s 1st project on the property. The firepit is below the waterfall.
The upper drive area
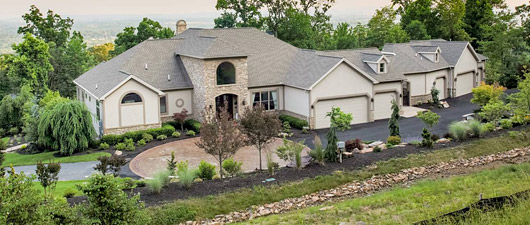
The rebuilt canal above the house is dry until the next big rain. The drive comes up from the left and delivers visitors to the paver circle at the front entrance. It continues on past the breezeway, the new garage complex to the right and around the side of the house for access to the backyard.
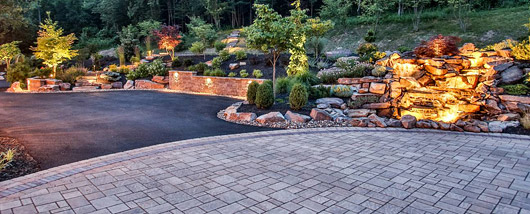
A landscaped berm, waterfall and retaining wall conceal the drainage canal. This is the view visitors see as they arrive at the front entrance after a tight turn from the wooded drive below. The asphalt pictured continues to the garages and beyond.

The old canal was about 4’ behind the face of the wall and only about 4’ wide. It was clogged with overgrown vegetation that dammed up when a big storm came. Water rushed over the top wearing down the backfill berm as hydraulic pressure pushed the wall over.
Tim says, “We moved the canal back 20’, made it a little deeper and widened it to 8’ or 9’. Then we planted grass so we could cut it with a Weedeater and keep it clear.”
Tim says, “We moved the canal back 20’, made it a little deeper and widened it to 8’ or 9’. Then we planted grass so we could cut it with a Weedeater and keep it clear.”
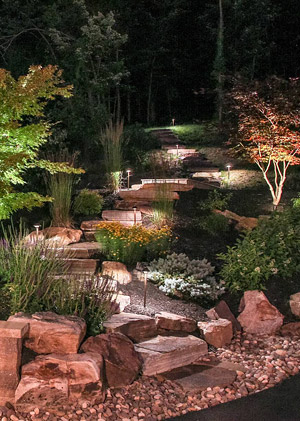
PA Landscaping built the canal bridge from a 26’ truck frame. Between the frame, lumber and man-hours, they finished the bridge for about $4,500. “We couldn't find anything that wouldn't cost an arm and a leg, so we went to the junkyard. The metal on the frame of the bridge was at least 3/8” thick. We sanded and painted it. It doesn't get a whole lot of weather since it's covered by the bridge, so it's going to be there a long time.”