Contractor Stories
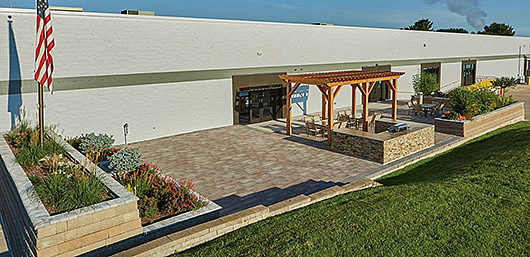
Carey had purchased hardscape materials to go with the brown building. Then the landlord painted it white. Fortunately the color scheme still works. The grassy area and the retaining wall in the grass (the one that’s not a planter) had to be left as is due to an easement for a nearby pipeline.
Knowing that the Church Mutual staff were going to build a pergola near the grill, Carey made sure there were no irrigation or electrical lines beneath the pergola area.
Knowing that the Church Mutual staff were going to build a pergola near the grill, Carey made sure there were no irrigation or electrical lines beneath the pergola area.
Taking the old Wal-Mart design challenge
Hardscaping on top of a badly sloped, cracked concrete slab that you can’t remove or damage.
By Tom HatlenProfile
Church Mutual expansion officeMerill, WI
Designer & Project Manager
Carey OwenColorscapes by Carey
Mount Pleasant, WI
Contractor
PICs Inc.Rhinelander, WI
Hardscape materials supplier
County MaterialsSize of improved space
4,500 sfProject value
$300,000In-house work
DesignExcavation
Pavers
Lighting
Landscaping & planting
Irrigation
Work done by subcontractors
Masonry mortar workElectrical
Carpentry
Structural footings
Year completed
2016The ink was barely dry when Church Mutual began the process of creating an outdoor relaxation space for employees. Designer/project manager Carey Owen says, “They are really keen on providing a welcoming outdoor environment for their employees. They have a similar area at their main facility with a Japanese garden and a waterfall.”
The space they had to work with used to be the garden center. It was a sunken, cracked concrete slab that drained towards the building. Metal fence posts had been cut leaving an inch or so protruding from the concrete.
And, because the facility was leased:
- They couldn’t take the existing slab out, and
- Anything they added onto the slab had to be removable without damaging the slab.
Turning a Wal-Mart concrete slab into a welcoming outdoor oasis was no easy task. Carey says, “Aside from the front doors, Wal-Mart’s have no windows. Like other Wal-Marts, this was a non-descript beige mass of a building. How do you take that and make it warm and inviting?”
Shifting parameters
Carey had worked with Church Mutual for years on past projects. But, to ensure honest pricing and fresh design ideas for this project, both the design and construction were put out to bid, but only to 1 other company. Carey says the client had very specific ideas for the walls, patio, the outdoor kitchen, the irrigation, everything. So, the designs weren’t an apples-to-oranges comparison.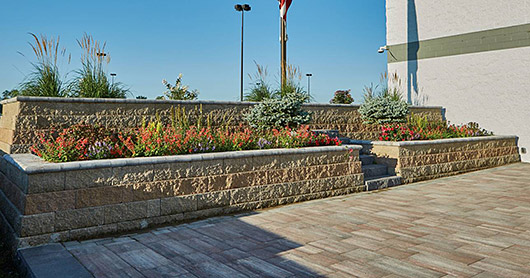
The 6’ wall screens off a parking lot. Like the other walls, it’s mortared to the concrete slab. But because it backs up to parking, Carey took extra steps to ensure it maintains structural integrity. The cores of the first 4 courses on the parking lot side are filled with poured concrete. And, there’s a layer of geogrid about halfway up that pulls all 4 walls of the planter together.
Carey says, “I've seen where somebody runs a car into a commercial wall and it just explodes the wall unit. They use loaders to clear snow on an area like this. If a plow hits it, we don’t want it to knock the wall over. How do you go back and fix a wall unit that's mortared to the ground?”
Carey says, “I've seen where somebody runs a car into a commercial wall and it just explodes the wall unit. They use loaders to clear snow on an area like this. If a plow hits it, we don’t want it to knock the wall over. How do you go back and fix a wall unit that's mortared to the ground?”
Her bid won. But, not long after, the project changed. The original parameters included the grassy lawn beyond the concrete slab. That’s where Carey’s design had placed footings for freestanding walls, a windbreak hedgerow of arbor vitae and other plant material.
Carey’s excavator was about to begin digging when he was stopped by inspectors representing a pipeline company that held an easement on the property. The inspectors were on site because there was a lot of other active construction on the exterior of the building, and their job was to monitor it.
The easement extended 100’ from the pipeline, and the concrete slab was 85’ from it. After 6 weeks of wrangling it was decided the existing slab would be grandfathered in and construction would be allowed on it, but absolutely nothing beyond that. No walls. No hedgerow. Carey says, “They wouldn't even let us plant an herb garden in there.
“So, now, how are we going to build this with nothing in the ground whatsoever? That's when we got the idea to mortar everything to the concrete. We tweaked the design and shrunk it up to make sure everything was on the concrete.”
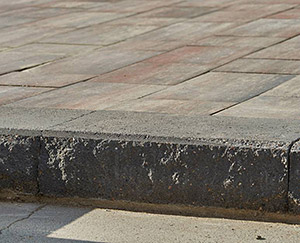
6” step units 75 lbs each were mortared to the existing concrete slab around the perimeter of the paved area. The units provided a comfortable step height for pedestrians and space beneath the pavers for irrigation and lighting lines within the sand and gravel base.
Mortar, the savior
The use of mortar on the slab was approved by the landlord as a product that was reasonably removable without damaging the concrete below. Carey says, “You could easily take a chisel to it, it would pop out, and you could reuse all the block.”When left unchiseled, mortar holds masonry blocks well. Mortar’s big advantage for this application was that the crew could build up the height of the mortar to level each block in the soldier course and the 1st course of wall block. Carey says the slope of the slab towards the building was so severe that they supplemented the mortar with up to 3”-thick pieces of block in some places.
Soldier course isn’t pavers
For the soldier course, they used 6” step units mortared to the slab. This solved a couple of issues:- The units provided a comfortable height step for pedestrians. Carey says using a typical 2-3/8” paver would have created an awkwardly low step and a tripping hazard.
- The taller soldier course provided space beneath the pavers for irrigation and lighting lines within the sand and gravel base.
The project began in late September 2015 after the 6 week delay. Walls, pavers, irrigation, lighting and plant material were in by the end of the year. The grill and kitchen area was completed the next spring. Carey was onsite constantly installing pavers, planting, doing whatever needed to be done while making sure everything was going to plan. Once her portion of the project was done, Church Mutual’s maintenance team then came in and built the pergola.
And, finally, in the fall of 2017, the project was chosen as the Winner of the HNA Award for Combination of Hardscape Products, Commercial less than 20,000 sf.
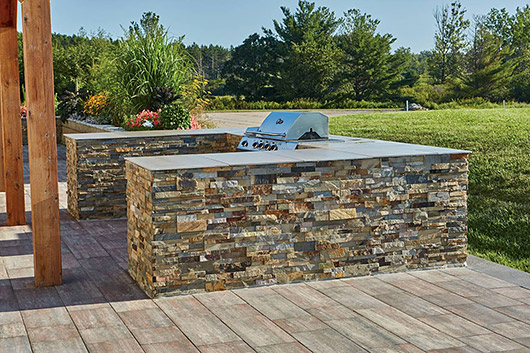
The grill was built on top of the installed pavers. At nearly 1,000 lbs, (with veneer and countertop) Carey says the structure isn’t going anywhere. Both the grill kit and Grand Milestone pavers are County Materials products same as the rest of the hardscape in this project.
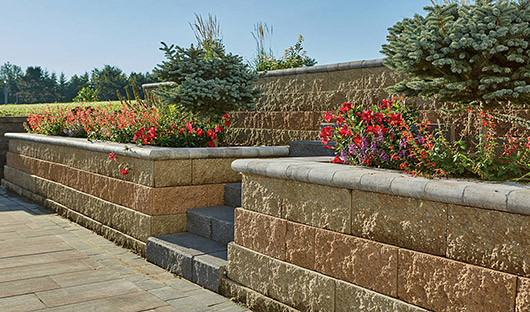
Carey chose a bull nose paver for the wall coping so that there wouldn’t be rough edges that might snag dress clothing or nylons. Steps built into the front wall give maintenance crews access to the second level to care for plants and to raise/lower the Flag.