Contractor Stories
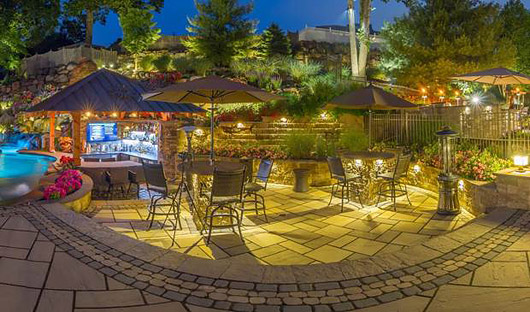
Building a backyard showroom
Contractor Joe Monello tells how he designed/built his backyard hardscape and uses it as a showroom.
By Tom HatlenJoe Monello’s backyard project earned Monello Landscaping 1 of the 2 Project Awards they received at this year’s Hardscape North America show.
Having the showroom at your house has its advantages:
- Your family gets to enjoy it so you’re probably willing to do more than you would for a display area at your facility. Who among us has a showroom at their shop at the level of what Joe has at home?
- Hardscaping your home creates very functional space that greatly adds to its value. Hardscaping a showroom by your shop in an industrial park might not count for much when you decide to sell.
Of course the drawback of having a showroom at your house is that you don’t want it open to the public. Joe says, “When the people are serious about doing a job with me, I'll invite them to come by. We don’t bring everybody over.
“We get a lot of jobs because we entertain so much. I've got 3 kids, and they each do at least 2 sports per season. They are on so many teams, and we always host the parties. Hundreds of people come over every year and they see the work I do. People are always saying, ‘Man, can we do something like that at my house?’"
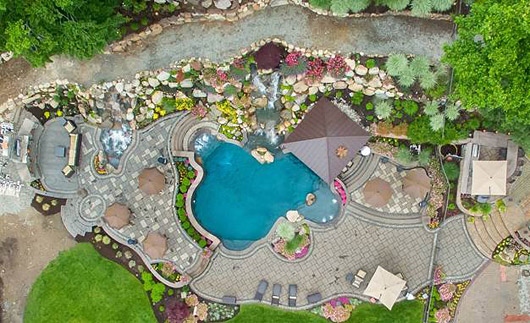
This photo shows the major entertainment areas. At the top, a 10’-wide road encircles the property and provides access for maintenance and future construction in addition to a place for kids to ride ATVs. The fire pit and bocce ball court are outside the picture frame. Joe says, “When we have parties, people congregate in all the different areas. There's so much going on, we could probably house about 300 people in this backyard and it wouldn't be crowded at all.”
Hardscaping his own property gave Joe an opportunity to show clients the possibilities they might be shy to choose otherwise. For example, he built a waterfall much larger than his clients typically request. He built a swim-up pool bar structure beyond anything he’s ever done before. He wanted to show prospects how much multiple levels can add to a project, so his project has 6.
Joe’s property also showcases new paver styles and mixed paver styles that people shy away from. Joe says, “A lot of people are hesitant to mix materials. They're worried about changing colors and textures, and trying new things. Worst case, if I try something at my house and it doesn’t work, I can always change it.”
10 years to remove the hill
Project Profile
Design/build contractor
Monello Landscape IndustriesWayne, NJ
Joe Monello, CEO
Size of improved space
1 acreProject value
Doesn’t want to knowIn-house work
Pavers/inlays/coping (5,000 sf)Waterfalls
SRW & boulder walls
Bar & outdoor kitchen
Fire features
Lighting & audio systems
Excavation
Work by others
Major excavationPool gunite & Pebble Tec
Plumber & electrician work
Some trucking
Year completed
OngoingWith the hill cut away, they built the boulder wall (with the big waterfall) along with a segmental retaining wall to hold back the remainder of the hill. From there, they installed the pool, irrigation and sod. Then came the bar.
“Building the bar held up the job for a long time, because it took so long between the engineering, the township, the approvals, the inspections, the cost. It was painful. Once we got that part done, we lived with it for the remainder of the season.” (See photos and read more about the bar construction issues in the following pages.)
“In the second year we were able to open up the pool. We put a roof on the bar. With no roof it got so hot out there. The day we put that roof on was a great day.”
In year 3 they finished out the project as it is now with the hot tub and the fireplace completed. Next, Joe’s planning to build a pool house, a storage barn, more fire features, and no doubt additional things to be decided later.
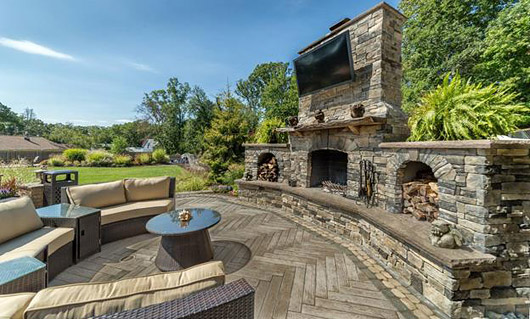
Hardscaping his own property gave Joe an opportunity to try new products and mix different materials. He says, “One of those was a new Techo-Bloc plank paver called Borealis by fireplace. I’d say 90% of the people who come over here think it's wood, but it's a paver. I thought it made a great accent.”
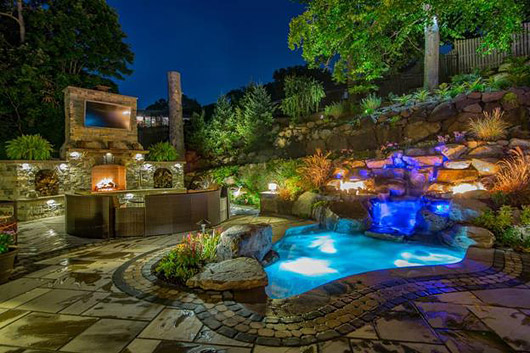
A waterfall appears to flow into the hot tub. The bright lights in the rocks above are actually fire features. Creative lighting produces the colors in the waterfall and tub. Joe says the tall tree stump behind the fireplace was spared for a reason. “I have a tree guy coming in January to carve bears into it. The bears will be climbing up that tree.”
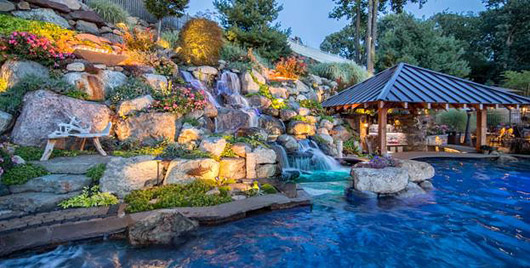
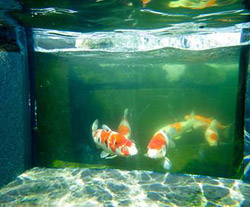
A 20’ waterfall serves as the centerpiece of the project. The waterfall is straddled by 38” ceramic fire bowls (high in the rocks) that sometimes shoot flames up to 18” high. The waterfall flows into the koi pond and appears to continue into the pool. Instead, it ends into 2 glass plates (lower right) that allow swimmers to view the koi from underwater. Joe had found that many clients are concerned with the liability and maintenance of a pond. But, experiencing the pond at his property puts them at ease and makes them want one. The same is true for the waterfall. “We don't have a lot of clients that do those big waterfalls because of the price. But people definitely like them, and we just sold a couple of big ones.”
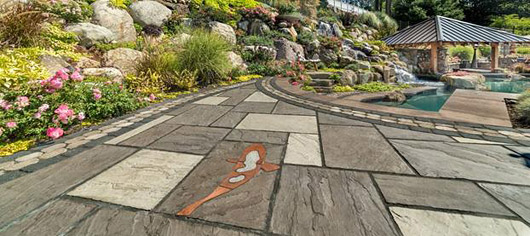
A series of fish inlays lead visitors across the patio to the koi pond.
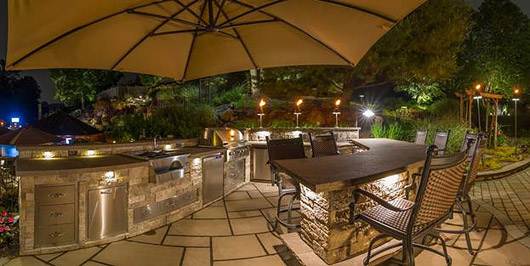
The upper kitchen is built from retaining wall block and a modular system with powder-coated stainless steel. Countertops are a unique leaded granite. Gas torches like those on the right side of the bar are posted all over the project. Joe says there are 20 of them with more to come.
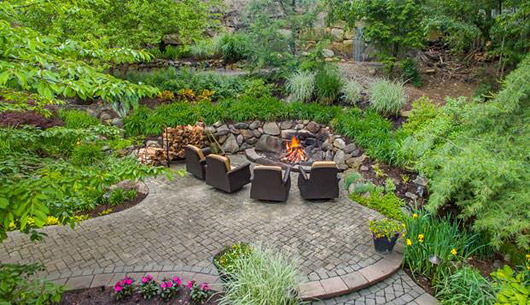
The fire pit area was one of the first things Joe built on the property. It’s placed somewhat remote from the pool area and is a fine place for kids to roast marshmallows.
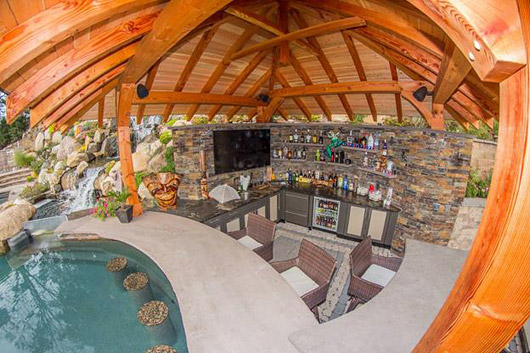
![]() | ![]() |
The bar floor is the lowest level of the project. It had to be low so that the bar stools inside the structure would be at the same height as the swim-up bar stools in the water. Making this happen was no easy task. In fact, Joe says building the bar cost more than building the pool.
When the crew excavated the area, it filled with water. To prevent this from being a regular occurrence, they dug it 6’ deeper than the bottom of the pool. Before filling the pit with drainage stone they dug a trench for a drainpipe. “It started at about 8’ deep. We had to trench the whole backyard to get that water out to daylight. Luckily, I had enough pitch.”
To hold back the hill behind the structure, the back wall was built of concrete reinforced with lots of rebar. The wood frame pictured was the form for the concrete wall.
When the crew excavated the area, it filled with water. To prevent this from being a regular occurrence, they dug it 6’ deeper than the bottom of the pool. Before filling the pit with drainage stone they dug a trench for a drainpipe. “It started at about 8’ deep. We had to trench the whole backyard to get that water out to daylight. Luckily, I had enough pitch.”
To hold back the hill behind the structure, the back wall was built of concrete reinforced with lots of rebar. The wood frame pictured was the form for the concrete wall.