Contractor Stories
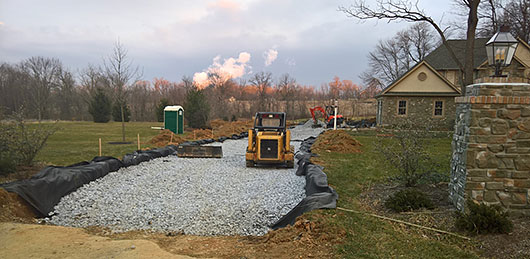
Photos show “True North,” Willow Gates Landscaping’s 2020 HNA Award winning project for Permeable Concrete Pavers. Jeremy says they installed 14” - 18” sub-base of #3 stone, 4” base of #57 stone and a 1.5” bedding layer of #8 stone. Joints filled with #8 stone.
Residential permeable systems get better & better
By Jeremy MartinPermeable interlocking concrete pavement (PICP) is a huge opportunity for us. Much of our work is in the Chesapeake Bay watershed, which has historically had a major issue with water quality. The federal government stepped in and set goals for reduction in contaminants.
While standards are set at the federal level, they are mostly enforced by local municipalities. And, while they rarely force changes to existing structures, they do require stormwater management when additional impervious surfaces are constructed such as buildings, driveways, and yes even patios.
Since municipalities (rural as well as urban) are required to reduce pollutants entering waterways, they are mandating that stormwater be contained to the property, or that runoff is greatly reduced.
From stone infiltration pits to PICP
We began encountering these issues in 2013. Our solution was simply to build a stone infiltration pit in the yard, and divert the downspouts from a roof area equivalent to the patio size we were installing. This system is absolutely effective; it’s also nearly invisible as it’s covered in topsoil and only has inspection and overflow ports visible. But it has zero value to the homeowner besides enabling them to get approval for the home improvement project they wanted.Enter PICP!!! What if we didn’t need to build a separate infiltration pit? What if our infiltration or detention area was actually our patio base? How could this not be the perfect solution?
Early on, client objections were mostly focused on the paver selection and the joint material. The first pavers marketed as being permeable? Let’s face it, they were ugly! And, most clients weren’t willing to deal with the loose gravel chips in the joints; it’s tough to blow off a patio with open graded stone joints without getting a few chips on the surface of the patio.
With time, though, we began to see more and more pavers being marketed as permeable. With the trend away from the 1/8” joints towards 1/4” joints, suddenly we had a huge variety of pavers available for PICP installations.
We experimented with joint stabilizing sealers to eliminate the stone chips coming out of the joints. The jointing market keeps evolving as well, with resin bound gravel and sand compounds offering easy-to-maintain joints that still flow a lot of water.
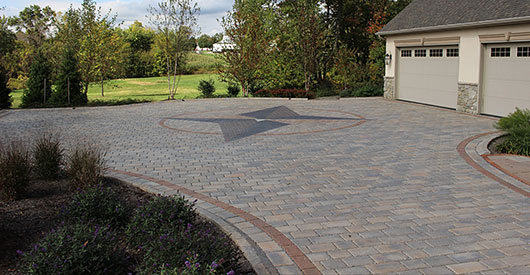
Embrace stormwater management
Rather than fight the stormwater management trend, we embraced it. I’m a numbers and technical kind of guy, and I loved the challenge of designing these systems. We began marketing for stormwater management, and reached the point that we can write the stormwater management plans in nearly all the areas we service. We use design software to determine base thickness when building driveways that accounts for soil type, rain events specific to that area, and anticipated traffic.Moving to hybrid installations
Along with this interest in stormwater management, in 2014 we were already installing what is today known as “hybrid installations” with open graded stone base and polymeric sand joints.This first began as a solution for raised patios, then we began using it as a way to install infiltration pits under a patio with sand filled joints and permeable paver drains (See the August/September 2019 feature in Hardscape Magazine for details). We also began using open graded base for 2 other key reasons: the ability to work in winter weather, and to allow polymeric sand to cure well in shaded areas.
We began to look at jointing options, and we started experimenting with wet sweep products. And as we began to explore these products, we learned that they were permeable. Early versions of these products were slow, expensive and best suited for joints 1/4”+.
These issues soon disappeared; the trends shifted towards slabs and we didn’t install many pavers with tight joints. The cost became a non-issue when we explained to clients the advantages.
We learned more efficient ways to install it; for quicker installs, I think the HydroBroom is essential. It’s not expensive, and every crew should have one! No, I don’t sell it or get a commission on it… it’s just the perfect tool for installing these wet sweep joint compounds.
These interests, trends, and obsessions all merged:
- PICP and stormwater management
- Installing through the winter, and using open graded base to facilitate year round work
- Wet sweep joint compounds for durability and permeability
Today, we rarely install a separate infiltration pit; we’re already building all our patios as partially permeable so there’s no need! We already use open graded base and permeable joint fill because I strongly believe that they’re better in the majority of installations. For us, there’s not much difference between a standard and fully permeable installation:
Standard (partially permeable) | Fully permeable |
Sloped and compacted subgrade | Level subgrade, no compaction |
Woven geo-textile | Non-woven geo-textile |
6”+ base | 8”+ base, sub base added for vehicular traffic |
Perforated pipe at lowest point in base to evacuate extra water from base | Pipe installed for extreme rain events |
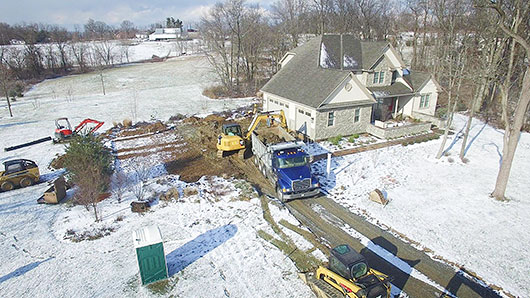
You see, we need a little more stone for our base. And we use non-woven geo-textile, which is a bit more expensive. Otherwise, there’s little difference. Additional cost is minimal for us to install our patios as fully permeable.
Most municipalities only require us to store 1” of rainfall in our base, and the most extreme is 4”. Open graded base has a 40% void space, so at a minimum we can store 3” in our fully permeable installations and easily exceed the requirements. PICP, this is your time to shine!
Some closing points:
- Some municipalities may require greater infiltration rates than achieved with these wet sweep compounds. In most systems, we expect to achieve 15” to 30” per hour through the pavers. While this far exceeds any storm, most PICP is designed with 100”+ per hour capabilities to allow for partial clogging.
- Wet sweep products can clog; permeability is restored by pressure washing. Because it doesn’t use the same maintenance methods as traditional stone chips, it may not meet PICP criteria.
- Some wet sweep products excel for patio applications, but aren’t strong enough for vehicular traffic. Do your research before choosing one for a driveway project. You will need to use a 2-part epoxy type resin for these applications.
Again, I reiterate that PICP opens up a huge residential market. It’s being driven by customer’s desires to be eco-conscious as well as legislation. With durable products that are attractive and similar to a typical paver installation, we offer a unique solution!
I mentioned that we market for stormwater management, and today we get many project inquiries specifically for this. Driveways are perfect for winter installations, and are always fun projects. Besides our local projects, I receive requests to consult on PICP projects out of state.
That, my friend, means that those states are under-served with contractors who are aware of the benefits of PICP and know how to market them. This is your opportunity!
Jeremy Martin co-founded Willow Gates Landscaping in 2005. He became an ICPI instructor in 2016, NCMA in 2018. He also founded Dust Killer Tools to help his company meet 2017 OSHA silica standards. Email Jeremy@DustKiller.tools. Visit WillowGatesLandscaping.com and DustKiller.tools
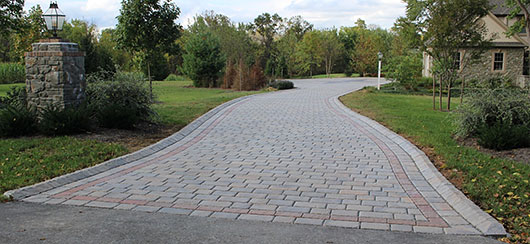