Contractor Stories
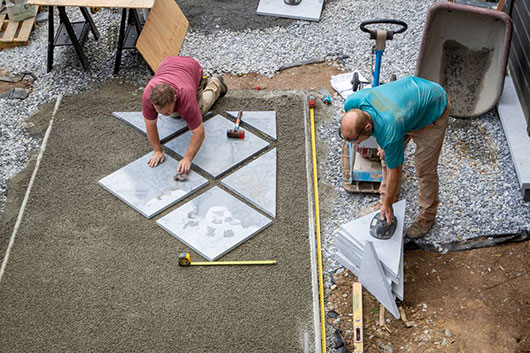
Keeping cool & organized under pressure
By Jeremy MartinIn recent months, I’ve written about integrity & authenticity and dealing with code officials. I’m beginning to believe that if I write about a topic, God’s going to send a test to make sure I really meant what I wrote! Will I hold to integrity when challenged? Do I really respect code officials? Some situations this spring were tough to work through, but I’m going to focus on one that taught us a few lessons.
The project was first discussed a few years ago, and early this year the client was ready to move forward. It was a small space, but personally I love that challenge. Sure, the 2,000 sf patio with the pool and big pavilion are impressive for their sheer scale, but anybody can create a large space. It’s the little spaces that I find the most rewarding, where we are literally fighting for every inch to deliver the customer’s dream while still meeting codes. These spaces take a lot more creativity.
This was a unique situation, as our project was being added to a building permit that had already been pulled for other renovations at this property. Although I wasn’t aware of it initially, this project would require approvals from 4 different municipal departments!
Changes from the beginning
A few weeks prior to starting the project, our supplier (who is good friends with my client) asked if they could do some video shoots demonstrating some new materials and installation methods. We worked out some design changes to utilize those products while ensuring the new materials would still be available in time and still work with storm water management criteria.This was a highly detailed project, despite only encompassing 1,200 sf. The lot was only 22’ wide, and we only had an 18’ x 20’ area to stage all equipment and materials. Day one, the client requested some changes to the design; his vision had changed and he wanted to tweak the layout. While this didn’t change the footprint of the area, it did change how everything was integrated and necessitated some complicated modifications. The elevation plan was completely rewritten.
Day 3, we requested an inspection of our excavation; Day 4, the response was a stop work order. Remember those 4 departments mentioned earlier? There was some significant miscommunication, and we learned we didn’t have full approval to start the project. It took a month, many discussions, and another complete design change to satisfy all the requirements. Certainly this tested my belief that code officials are our friends!
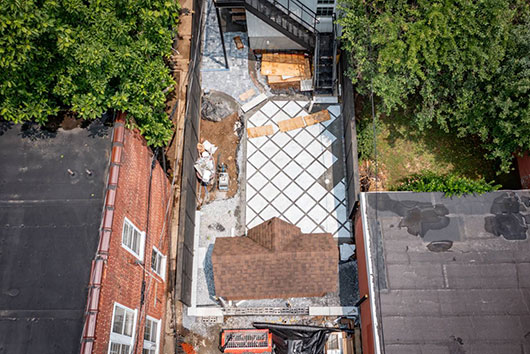
Working in a very confined space.
Problems
Once work finally resumed, the challenges continued. The elevation plan changed after a benchmark had been marked, which affected most of the project. But, the physical benchmark wasn’t updated. The error wasn’t discovered until late in the project. While it didn’t create a major issue, it was one more thing to resolve.Then we were pushing to have the project ready for the video shoots, as we had to coordinate the videographer, supplier and materials. In every step of the project, we struggled with tight access and limited street parking. We pushed as hard as we could within the tight limits of the project. Then we were installing products that, while we’ve dabbled in them previously, are definitely not our normal. And we struggled to maintain efficiency and quality control.
When everything goes awry and the pressure is on, what happens? I’ll tell you what happened for us. We started letting little things slip. Crew meeting? Postponed. Weekly cleaning of the job trailer? Eh, we’ll get it on a rainy day. Tools kept carefully labeled and in their place? The new guys on the crew didn’t understand the system and scrambled everything. This cost time and frustration.
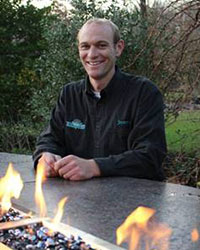
Jeremy Martin
Who’s at fault?
How do you recover from this? It’s tempting to blame everything but ourselves. There were external factors, the design changes, permitting nightmares, and coordinating with the videographer. Then there were the internal factors too. I could blame the crew or the foreman for letting some of these things happen. When you find yourself between the proverbial rock & a hard place, or in our case between some Turkish marble and Chinese sandstone, what do you do?Recognize root causes. I think it’s important to understand the distinction between recognizing causes and playing the blame game. For example, we were asked to change materials for the video shoot, and indeed that cost a lot of time.
Also, the client requested a certain paving pattern. Accommodating that change ended up being one of the most difficult parts of the project. In retrospect, I should have told the client we couldn’t do it. But I was too stubborn to heed some warnings and pushed forward.
In case you wanted to know, 4” x 8” herringbone with no spacer bars … in a wet lay application … with multiple people … makes it tough to keep straight lines, and there’s no adjusting them after the fact.
The project also affected my life outside of work. There was an onsite meeting I attended when I promised my children I’d take off early to go to an annual car show. I couldn’t control that it went much later than I expected and left us with only a short time at the show. But, I could have and should have simply said sorry, I can’t attend. Getting angry at the result (arriving just as the show was closing) ignores my role.
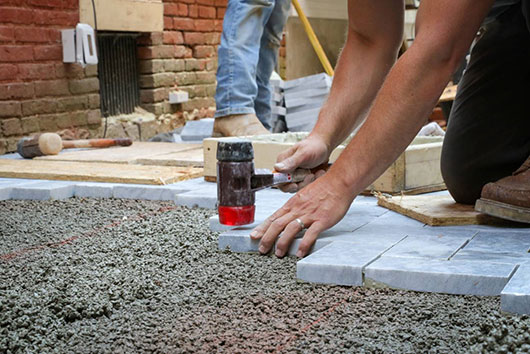
The client requested a herringbone design with 4” x 8” pavers and no spacer bars in a wet lay application.
Deal with it
We all deal with problems, but rather than blaming everybody else, it’s good to step back and analyze how we ourselves could have better managed the situation.Put a lid on the voice in your head that tells you to lash out. Would you be friends with the voice in your head? Probably not on a bad day, and most certainly not with the voice in my head during those long weeks. It had plenty to say about the situation in general and myself in particular. Brooding over problems or beating yourself up doesn’t solve issues, it just keeps your mind too busy to focus on solutions.
Build up your crew. Times like this are hard on morale, and require care when addressing shortfalls. Near the end of the project, we simply took a morning off for that overdue crew meeting. We went out for breakfast, then reviewed the processes and standards that had been declining.
We identified problems and how we needed to address them, while acknowledging the pressure we’d all been under. We better explained our system to the new crew members, cleaned & organized the job trailer and trucks, and had a fresh start for the week and for the next project.
We need to seek the patience of Job and the wisdom of Solomon. We need to hold ourselves and our crews accountable for mistakes. Without that, we fall into disorganization and frustration. Yet we need to avoid destroying morale or self-confidence in the process! It takes a generous amount of patience and wisdom to walk that line.
The next project on our schedule? All flatwork, 10-acre rural property with no neighbor in sight, and all straight lines. It’s going to be a vacation!
Jeremy Martin co-founded Willow Gates Landscaping in 2005. He became an ICPI instructor in 2016, NCMA in 2018. He also founded Dust Killer Tools to help his company meet 2017 OSHA silica standards. Email Jeremy@DustKiller.tools. Visit WillowGatesLandscaping.com and DustKiller.tools