Construction articles
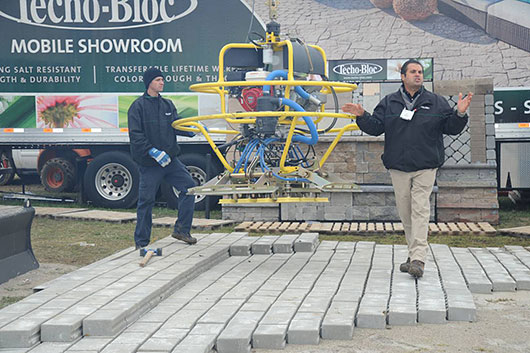
Techo-Bloc’s Pete Baloglou (right) has been inspiring
contractors for over 25 years.
contractors for over 25 years.
Filling joints in segmental pavements
By Pete Baloglou, Techo-BlocSegmental pavements have a 7,000-year history of success. They have evolved from rough fitting stone to manufactured units made indoors under controlled conditions to strict durability standards.
The type of segmental pavement unit available has expanded from tightly fitted block units (Interlocking Concrete Pavements – ICP) to also include large format Concrete Paving Slabs (CPS), Plank Stone (PS) and Segmental Permeable Pavement (SPP) the last of which allows storm water infiltration.
Over the years joint filling techniques and products have expanded and advanced as well. Different characteristics and specifications are relevant to transfer of energy (loads), drainage, aesthetics, long-term care, keeping storm water run-off on the surface, infiltration and filtration.
With so many benefits, it’s best to look at jointing material such as Washed Concrete Sand (WCS), Masonry Sand, with or without joint stabilizing protectant, Polymeric Sand, and Jointing Compounds first. Then we’ll discuss the economic and environmental advantages of open, poorly graded aggregates like ASTM #8 and #9 stone with or without joint stabilizing protectants for Permeable Pavement.
Options for ICP, CPS and PS include:
- WCS
- Masonry Sand
- Either of the above with Joint Stabilizing Protectant
- Polymeric Sand
- Jointing Compound
Washed Concrete Sand, ASTM c33, (also used in the manufacture of concrete) has been the industry approved joint fill since ICP’s inception post World War II. Its course, angular, large (for sand) particles with less than 5% passing the 200 sieve make it a natural choice for drainage and vertical interlock.
Vertical interlock (sand in the joint) won’t allow a paver to move independent of its tightly fitted (1/16” to 3/16”) neighbor, commonly called shear transfer of energy. WCS’s gradation makes it time consuming to get into the joint, but it stays in longer and is a strong option.
Masonry Sand, ASTM c144, is rounded and sized with up to 5% passing the 200 sieve typically used in mortar for masonry projects. This sand goes into the joint quickly and cleanly. Cost is low and availability high making this choice an industry standard.
Tying together WCS and Masonry Sand can be a joint stabilizing protectant. These breathable, penetrating, often stain resistant and color boosting protectants help bind jointing sand together with a mix of siloxane and silane (a hybrid) while caring for your pavement investment. Joint stabilization and pavement finish protection for 1 to 3, 3 to 5, 5 to 10+ years depending on environment and traffic is a great 1-2 punch.
Like Jake Boyer of PROSOCO points out, “Joint Stabilizer not only provides protection to the sand joint by consolidating loosely bound sand particles, preventing weed growth and joint degradation, but also to the surface of the pavers, providing long lasting water and stain repellency.”
Polymeric Sands are polymer enhanced, water activated ASTM c144 sand that is bagged and ready for joint fill. Many options exist on the market with differing features, benefits and value. Advantages of bagged dried products like Polymeric Sand are staging, production and low waste ratios.
Finally, Jointing Compound is a wet-purchased (in buckets) and applied joint fill for typically wider joints (3/16”-1/4”+) that still maintains interlock. Products exist for pedestrian only and for vehicular traffic, so read the label and seek consultation. All weather (above freezing) is this option’s key advantage and application.
The joint fill for Permeable Pavement should be ASTM #8 or #9 stone depending on spacing. ASTM #8 (3/8” to 1/4”) clean stone is ideal for joint spaces from 1/2” to 1”+. ASTM #9 (1/8” to 3/16”) clean stone works for 1/4” to 1/2” tighter jointed systems.
Both have 90% fractured face, less than 5% passing the 200 sieve, are hardness tested, with a narrow, poorly graded range of particles. A solution these aggregates offer for Permeable Pavers is the almost infinite receptor points each stone possesses for filtration of contaminates.
Contaminates like TSS (Total Suspended Solids), Organics, Petroleum Distilates, Heavy Metals like brake dust, etc…. attach to the receptor points and can be aggitated and removed to increase infiltration if water puddling is observed. Open graded joint fill also generates microbes that will consume these harmful contaminates. Clean stone can be a great color and texture enhancement to the paving product.
These ASTM #8 and #9 course angular particles remain securely in the joint especially when subject to microscopic airborne particles even on steep slopes, snow plowed areas, pool decks, etc. But a joint stabilizing protectant can assist. In addition to joint stabilization these Protectants benefit deicing salt resistance, ease of long-term maintenance and breathability, representing a tremendous value with very little reduction in infiltration.
Joint filling, as we’ve seen, isn’t just a sweep, wet and run process. The focus on this final detail of installing a segmental pavement can be the difference between success and failure. Joints filled, consolidated and stabilized allow segmental pavements to provide a lifetime of enjoyment.
Pete Baloglou is a Sales Coach and Techo-Bloc's North American Director of Education and Information. You can find him on Facebook @PaverPete1. Email PaverPete@Techo-Bloc.com. Visit Techo-Bloc.com.