Contractor Stories
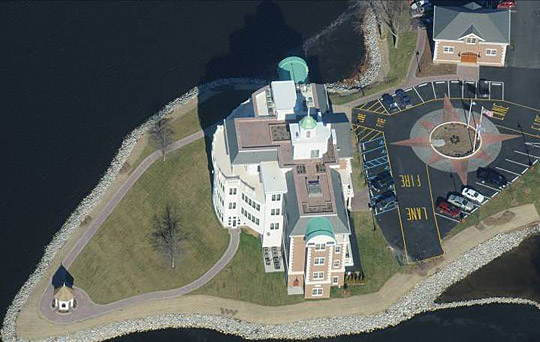
Compass Pointe roof pavers
Education/experience win invitation-only bid to build on a roof and on the turf.
By Tom HatlenThe Brick Doctor President Reggie Capitan says they've worked on projects like Compass Pointe before, "but that was the only one 5 stories up in the air." The project also involved work on the ground installing a 2,251 sq. ft. custom-designed compass rose and a paver path out to the point. By the time it was done the Compass Pointe project had doubled in value from the original design that Reggie had bid.
The invitation to bid went out to a short-list of contractors, and came from a landscape architectural firm that had worked with The Brick Doctor a lot in the past. "They call us a lot when they're trying to turn their ideas into reality, and they say, 'Hey, can we do this? Will this work?' They know I'm involved in the ICPI and keep up with the industry and with the current standards."
Growing the job
With the bid won, and the contract secured, they prepared to begin work. Up to this time, the building owner had let the landscape architect serve as the chief contact for the project. But once on site the owner stepped in, and that's where the add-ons came into play.The owner had more of a personal connection to the project because he planned to use the top floor and rooftop as his personal living space above the high-end office space and restaurant below. The building was a new construction designed to fit with nearby historic downtown Dover, DE.
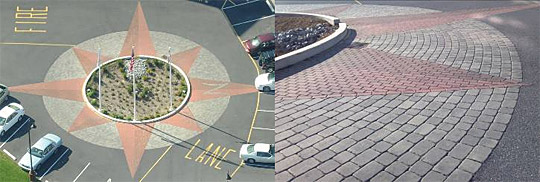
2 slightly different colors of pavers were used on opposite sides of the points to make them appear 3 dimensional. The Brick Doctor laid out and cut the compass rose themselves. Building a symmetrical feature like this requires near perfection in the layout or people will notice. Reggie says Jason's experience was invaluable in getting this done.
"He was very impressed with the work he saw us doing. So as we suggested things he was very receptive." Reggie explains, "I had a great site manager there in Jason Goodnight. He was key to the add-ons. I wish I had 10 more of him."
Jason is ICPI and NCMA installer certified, has 15 years with The Brick Doctor and experience with poured concrete before that. So, Jason offered an excellent perspective to help the owner realize the potential for his property.
Add-ons included the paver path on the ground plus these additions to the rooftop: expanded patio, the hot tub walls, the planter walls as well as the coping and SRW veneer on the parapet walls. The original plan was limited to the compass rose and part of the rooftop paver area.
Installing pavers on a rubber roof
Hardscape construction started on the rooftop first since the paver pathway wasn't yet planned, and the compass rose area needed to be open for contractors finishing the building's interior.Paving the roof had more similarities to an in-ground paver installation than you might think. The roof was designed to hold the additional weight of the standard 2-3/8" concrete pavers and a sand setting bed. The geo-textile used is the same product The Brick Doctor uses on the ground for applications like separating drainage rock from soils.
In some ways installing on the roof was easier. No excavation. No questionable soils to worry over. No base to install or compact. The parapet walls served as ready-made edge restraint on all sides.
So, what was more difficult? Aside from dealing with the element of danger, the roof had multitudes of elevation changes for drainage which had to be modified to accommodate pavers. Plus, you couldn't cut pavers in place or drop/toss anything for fear of tearing the roof. And, it took more than trucks and loaders to move materials, tools and equipment to the worksite.
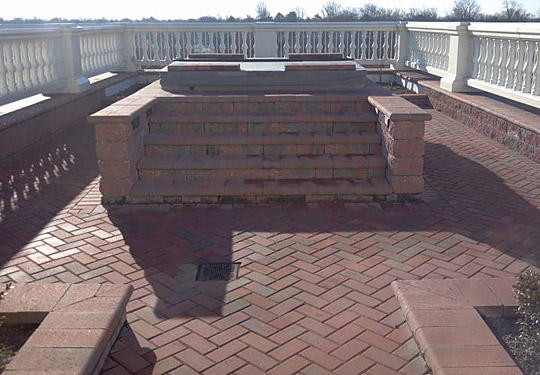
The entire hot tub/planter area was not in the original design that was bid. Wall lights illuminate the hot tub steps at night.
Don't damage the EPDM
Naturally, the roofing contractor was concerned about a paver installation on his work. So he tested the "EPDM" synthetic rubber roofing before The Brick Doctor started their work. Reggie explains, "They actually blocked the drains on the roof and put 6" of water on there to make sure the EPDM's not leaking. Then if it leaks after we've been up there, it's on us. We're going to be liable for the water damage it causes and for fixing the roof."Normally The Brick Doctor crews do a lot of their cutting on the ground with pavers in place. To avoid damaging the roof all cutting had to be done with a table saw, or on a bench. They also had to be careful not to drop anything.
"If you dropped one of those 16" Coventry blocks, if it hit on a corner, I guarantee it would have punched through the EPDM. We had to stress to our guys daily: 'If you drop something, let Jason know so we can make sure there isn't any damage to the roof. If we catch it now we have the roof guy come in and he puts on a patch. If you hide it, they're going to see it when it rains and then we're going to have a problem.'"
Project profile
Compass Pointeon Silver Lake in Dover, DE
Hardscape construction company
The Brick Doctor, Inc., Dover, DE
Reggie Capitan, President
Jason Goodnight, Vice President
Design company
Landscape Architectural Services, Viola, DE
Matthew T. Spong, RLA, ASLA
Original hardscape construction contract
3,826 sq. ft. pavers (compass rose & roof pavers)
450 sq. face ft. split face wall, planters and steps
Change orders
1,170 sq. ft. pavers (paver path plus additional roof pavers)
815 sq. ft. bullnose pavers (installed for parapet wall coping)
160 sq. face ft. split face wall utilized for parapet wall riser
Hardscape project value
$129,000 ($62,000 original + $67,000 change orders)
In-house work
Ground level – Installation of paver base, geo-textile, setting bed, edging base, edging, pavers
Roof top – Installation of geo-textile, setting bed, retaining walls, planters, custom hot tub enclosure with wall lights, parapet wall bullnose and risers
Work done by others
Non-hardscape structures and landscaping
Year completed
2008
Getting everything up there
Reggie says the biggest challenge of building on the roof was getting material, equipment and people up there. He said the building's elevator wasn't rated to lift anything close to a 3,000+ lb. pallet of pavers, and it wouldn't have been productive to bring up small amounts of materials at a time. Instead, they rented a crane and operator to lift all heavy materials to the top. They attached a concrete bucket to carry sand to the top, and they attached forks to lift pallets of pavers and wall block.To keep crane costs down they carefully calculated which days they would need it and how long each day. Reggie says, "The rental place was able to tell us, for example, that on a typical reach up to 60', it would take 8 minutes per cycle or something. That bucket holds X cubic yards of material, and if we needed 3 cubic yards up there, we could calculate how long we'd need the crane there."
The Brick Doctor also rented an all-terrain aerial lift that Jason operated. The lift stayed on site to get tools to and from the roof every day. Sometimes they used the lift to carry people. In hard to reach areas it was much easier to install the coping for the parapet wall while working from outside the wall in the lift.
Maybe 50 elevation points!
While this roof was strong enough for pavers, it was built for drainage. In this case there were 12 different drains in the paved area. In each of those 12 drain areas, the roof is re-sloped on 3, 4 or more sides down to the drain. So they might have had 50 elevation points to deal with.Getting the paver herringbone pattern to merge well from one area to the next required some finagling. In areas where the elevation changes were too extreme they made up the difference by varying the depth of the sand bed.
"We couldn't just use a 1" screed and pull everything off. To make the elevations more consistent, we might use 1-1/2" of sand in one part of an area and transition it down to 3/8" of sand in another part. It's doable, you just had to work it out."
They might work it out by cutting a piece of lumber that angles from 3/8" at one end to 1-1/2" at the other. Other times they might prop up a piece of pipe to get the heights they want. Some areas just had to be hand-floated and adjusted by someone with an experienced eye like Jason.
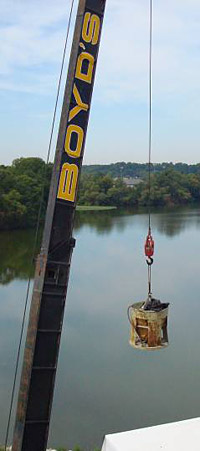
A rented crane with a concrete bucket carried sand to the roof. They replaced the bucket with a pallet fork attachment to lift pavers and wall block.
Words of warning
1. No railing was required or installed when The Brick Doctor paved the roof. So there was no room for "getting caught-up in your work" and not thinking about where you were.2. Rubber roofs bounce. As the crew laid more pavers, the uncovered part of the roof became unnervingly bouncy, so much so that Jason and Reggie became concerned about the roof holding up. A structural engineer's inspection of the girders supporting the roof determined that the deflection on each beam was well within tolerances, so the installation continued. Reggie says, "Once we were done and everything was in place it calmed down a lot. It's nothing like it was. It was like being on a diving board."
Returning to Earth
Back on solid ground the crew started work on the compass rose. Reggie says the site excavation contractor installed a gravel base for them. But Jason learned that only 4" of base had been specified and installed. After explaining how 4" would not hold up on a commercial application like this, the owner agreed to cover the cost of The Brick Doctor redoing the base to a depth of 10".They had the asphalt contractor over-shoot the compass rose boundaries by about 5" all the way around. Then Jason's crew could cut the asphalt out in nice clean, straight lines and use the asphalt as the edging. They laid out and cut the compass rose themselves.
Installing the paver path around the point was done last as an add-on. It was a standard paver installation. Good coordination with other contractors and suppliers allowed them to complete the job in 6 weeks without any real breaks in action.
Today, Compass Pointe is a show place of The Brick Doctor's work. Reggie says the roof should actually last longer than the EPDM's 25-year-plus rating because it's protected from UV rays and weather that would degrade it.
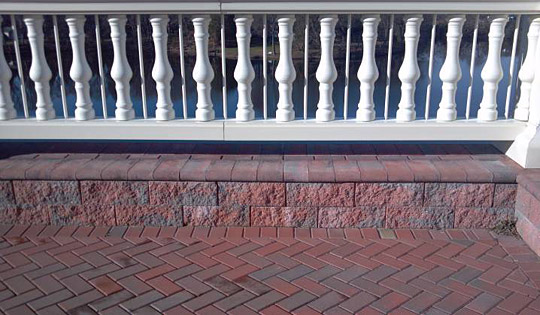
The double bull-nose coping and retaining wall veneer on the parapet walls of the roof were an add-on to the job. They created the wall veneer by cutting the face off of split-face block. The white railing was added later by an outside contractor.
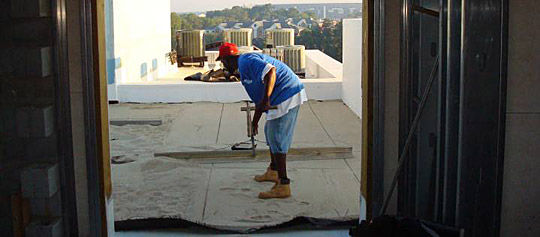
Sand on the roof couldn't always be screeded to a standard 1" depth. Sometimes the elevation change from one drainage area to another was too abrupt for a smooth paver installation. To compensate, they varied the depth of the sand bed from a minimum of 1/8" to a maximum of 1-1/2".
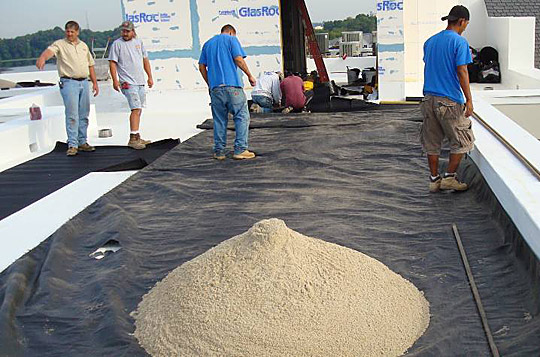
Geo-textile was laid over the roof to prevent sand loss down the drains.
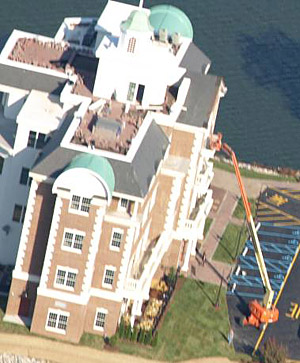
The Brick Doctor rented an all-terrain aerial lift to get tools to and from the roof every day. The lift also carried crewmembers allowing them to access hard-to-reach sections of the parapet wall and install coping.
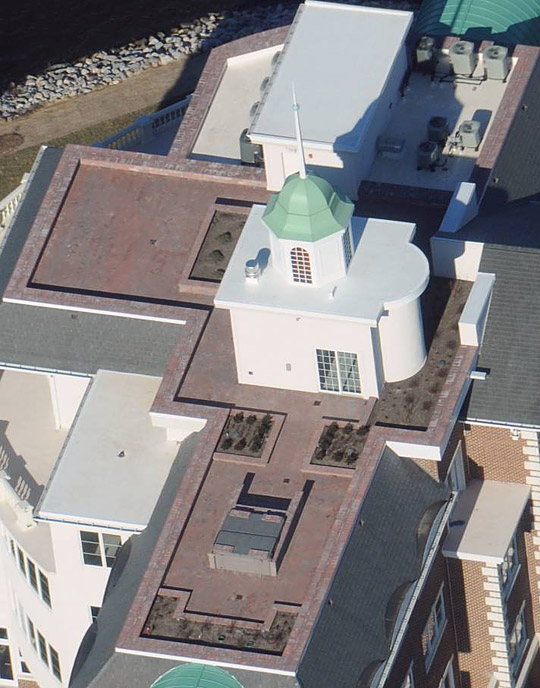