Contractor Stories
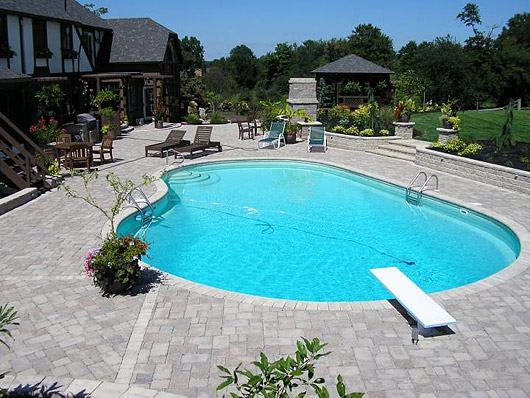
Loyalty, honesty and integrity pay off
Gaining referrals through loyalty; winning work thru honesty and building with integrity.By Tom Hatlen
Eberhardt Landscaping had been buying all their plant stock from the same nursery for years. This wasn’t lost on the nursery’s owner when he needed a landscaper to regularly handle installation work that comes in.
“He told me, ‘You’ve been a good customer for us. You’ve got a good reputation. Bill, if you can handle all the work, you’ve got it,’” reflects Bill Eberhardt. “Well, we made sure we could handle it all. For the last 14 years, they’ve sent all their landscape work to Eberhardt.”
Today, Eberhardt has a display at the nursery with a patio, a retaining wall planter for nursery stock, and some furniture so people can enjoy the area. A nursery referral last year led to one of Eberhardt’s largest jobs ever, a hardscape project that included a built-in grill and built-in fireplace – both were features Eberhardt had the expertise to build, but which they had yet to be hired to build. They just needed the right customer.
ProfileEberhardt Landscaping, Barberton, OHFounded 1987 Bill Eberhardt, Owner/President Brad Wilson, Landscape Operations Manager Customer base 60% commercial 40% residential Services mix 70% maintenance 30% landscape installation Number of employees Seasonal, 12 to 18 ProjectPrivate residence, Northeast OhioIn-house work
Subcontracted work
|
Give ‘em what they want
At Eberhardt, Brad Wilson is the “go-to guy” when calls for landscape construction work like this come in. Brad met the client (call him Carlos) on site and saw that the property was one of the more fabulous estates in the area. Carlos appeared knowledgeable and specific about what he wanted. So Brad listened carefully, and at the next meeting presented a design sketch and pricing.
“I was about half way through the specs on the project and he started smiling. Then he told me why. Having seen this great property, the other 2 companies bidding had added lavish features he didn’t ask for like a putting green around his pool. He wasn’t a golfer. He said, ‘I liked that you took everything that I pointed out and didn’t embellish on it to see how much money you could make off this property.’”
It’s funny how things sometimes work themselves out. While Brad won the job by listening and not pressing for an up-sell, the job nearly doubled in size after the contract was signed. As the project was taking shape the customer saw the potential and agreed to expand the project from 4 weeks of work to 7 weeks.
The impostor is revealed
Brad was waiting at the Eberhardt office for the meeting to finalize contract details when Carlos arrived – and revealed his true identity. He was not the homeowner. He was the owner’s long-time friend and landscaper. The hardscape work was outside his area of expertise so he had been serving as the homeowner’s representative and advisor. The homeowner (call him Mr. Wentworth) would arrive shortly.“I had about 15 minutes to get my head wrapped around that, and to refocus,” says Brad. “I decided I should rehash everything from the beginning. I couldn’t assume that Carlos had passed everything on.”
The meeting went well. Mr. Wentworth was an attorney and was most interested in costs for what he was getting. Brad says, “Great guy to work for, but you definitely want to keep him in the loop. So from day 1, I kept in contact with him every day. First I would call Carlos and say, ‘This is where we’re at on the project. This is where we want to be tomorrow.’ Then I would call Mr. Wentworth.”
![]() A little accent color for the soldier course, wall caps and pool coping goes a long ways. |
Construction commences
The initial 4-week plan included installing 3,300 sq. ft. of pavers around an existing swimming pool, all the retaining wall, 3 sets of landings/steps and the built-in grill and fireplace. The additional 3-weeks of work involved adding a lower patio, more steps, wall lights throughout and some pillars.Job 1 was to remove the existing poured concrete pool deck and connected walkways. The deck was just an 8’ ring around the pool, but demolishing it without also demolishing the pool was a concern. So Brad brought in an experienced subcontractor they often use to break-up the concrete and haul it away.
“It takes a lot of risk out of the job,” explains Brad. “He does things like this day in and day out so he really knows how close he can get with the skid steer, and how to work the jackhammer so it doesn’t damage the pool. We’ve found they can do things like this a lot more quickly and efficiently than we could. He had it out of there in a day.”
The next day the Eberhardt crew began digging with a rented mini-excavator, and moving the dirt with a skid steer. They had to be careful not to over-dig around the septic tank which was just 8” down. The patio was to be built over the septic just as the concrete patio before it had been.
They were still excavating when the customer agreed to the additional paver, step and pillar work. This worked out well for coordinating with the rest of the job. Access for equipment was wide open, and the property had a spot in need of fill where they could dump the 80 to 100 tons of spoil from the site.
Brad says he was 3 days into the project when they started putting in new material. They installed base for the retaining walls with the gravel extending out far enough that wall builders wouldn’t be standing in mud.
They built the wall and steps until they were about 90% done. An area planned for the fireplace was left open because the customer had wanted to see how everything was going to flow together before deciding the exact placement for the fireplace. Since the question was a matter of 3’ to 5’ one way or another, the gas lines had already been run to the general area just as they had been to the grill area.
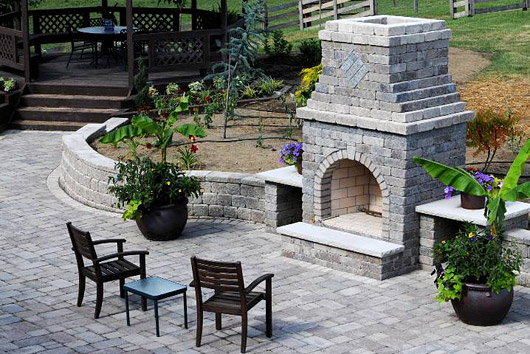
Eberhardt built the fireplace from a Unilock kit, but the simple firewood boxes were custom built to suit the customer’s wishes. Installing a heavy, mortared fire feature like this required footers down to the frost line to support a slab the length of the fireplace. The crew put four 1’ diameter, cardboard tubes 3’into the ground. To each tube they added rebar that extended out of the hole a few inches into the slab. Then, in one pour, they filled both the tubes and the slab forms. From there Brad says it was pretty simple to cut, glue and mortar pieces together from the kit. The tubes stay in the ground.
With good advance communication to the customer, the placement decision was made promptly. So they finished up the wall, poured the fireplace foundation and followed the kit instructions for building the balance of the fireplace. While the grill wasn’t built from a kit, the construction process was similar.
The crew couldn’t install the paver base back when they did the wall base because the customer’s pool contractor needed access to lines buried in the area. Now, they installed the paver base with geo-textile below it. Area soils are largely clay so they use geo-textile as a standard practice on paver jobs. Installing the base helped establish the elevation for 2 septic access covers Brad needed to construct within the patio. For the covers, pavers were affixed to a metal lid and placed over a concrete-lined hole that provided access down to the tank cap.
Pavers came next followed by wall lights and wall caps. Brad says the lights were the last major addition to the original plan. He and Carlos were looking things over one day as the final phase of construction was wrapping up. “It was late in the day, and getting dark. I said, ‘You know, accent lighting would do this a lot of justice.’” And no one could disagree with that.

The wall lights were the last major addition to the original plan.
![]() These steps and pillars were an addition to the original plan. The patio/pool area is lower than the hill behind the house necessitating the retaining wall for the length of the patio. |
![]() Brad says the customer wanted a simple structure for the gas grill so building it was fairly simple too. They poured footers and a slab just as they did for the fireplace (see fireplace caption). Then they glued a concrete box leaving enough space for the grill insert to fit according to the manufacturer’s specifications. The doors open to a storage area, not an oven. |
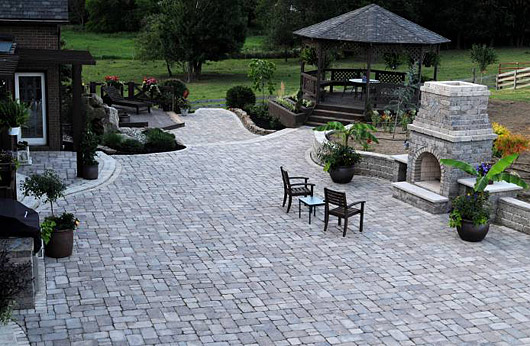
The lower patio in the distance was an addition to the original plan. The gazebo and deck off the house were existing features.
![]() Raised planters separate the pool area from the drive. Eberhardt installed the soil and larger plants as well as the walls. In the patio, a “V” of pavers pointing to the pool serves as a transition line from the fixed height of the pool down to the fixed height of the entry. |
![]() |